WORK ORDER MANAGEMENT
SOFTWARE MODULE
- service requests,
- nonrecurring corrective repair work orders, and
- recurring preventive maintenance work orders.
MAINTENANCE
"Many programs are well defined, but sometimes they don't include all the key components that we cover in this guide."
Jorma Manninen, Chief Marketing Officer
ANEO Software Oy
.png?width=720&height=1040&name=2021-12-20%20Lead%20Generator%207%20Steps%20(ENG).png)
BENEFITS
REPAIRS
INSPECTIONS
MAINTENANCE
MAINTENANCE MANAGEMENT
SERVICE REQUEST
STARTER
ANEO Zero Starter contains the necessary features for managing service requests. Operators and other ticket users can create service requests on the spot based on detected faults and failures or observed hazards and incidents in the field.
The ticket user creating a service request selects the object, writes or dictates the job description, selects the level of urgency and can also add a photo or other attachments from the memory or clipboard of the mobile device or computer or select files already saved in ANEO Zero.
PROFESSIONAL
ANEO Zero Professional includes the same features as Starter. In addition, the required data fields of the service request can be configured according to the customer's needs.
Maintenance planners can search for service requests according to the type of service request and create new repair work orders from the service request. The information saved in the service request is copied to the new work order.
ANEO Zero automatically attaches the service request to the new work order created based on the service request.
ENTERPRISE
ANEO Zero Enterprise includes the same features as Starter and Professional. In addition, workflow automation enables the creation of a new work order automatically based on a new service request.
For example, if the urgency level of a service request or another classification category requires it, a new work order can be created automatically.
ANEO Zero automatically attaches the original service request to the new work order, which speeds up the planning and execution of the work order.
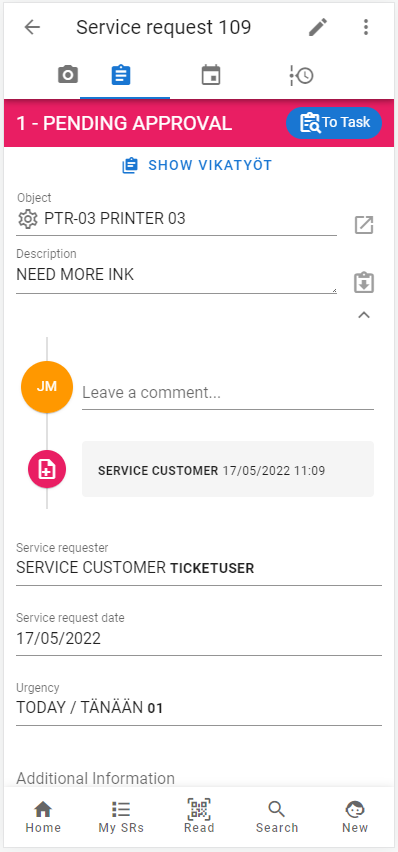
STARTER
STARTER
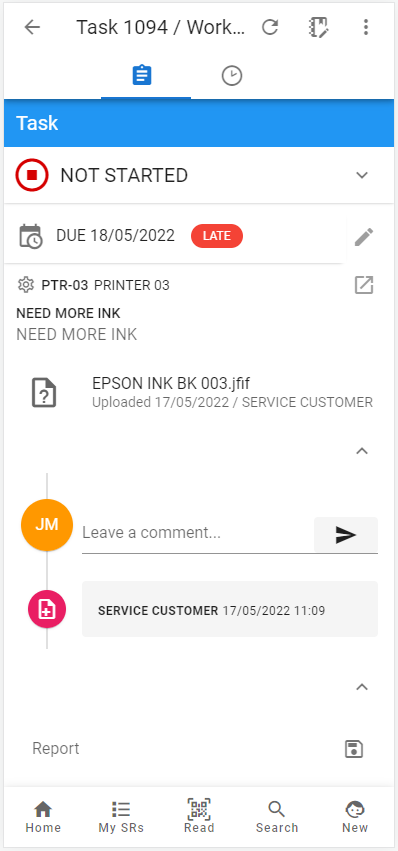
PROFESSIONAL
PROFESSIONAL
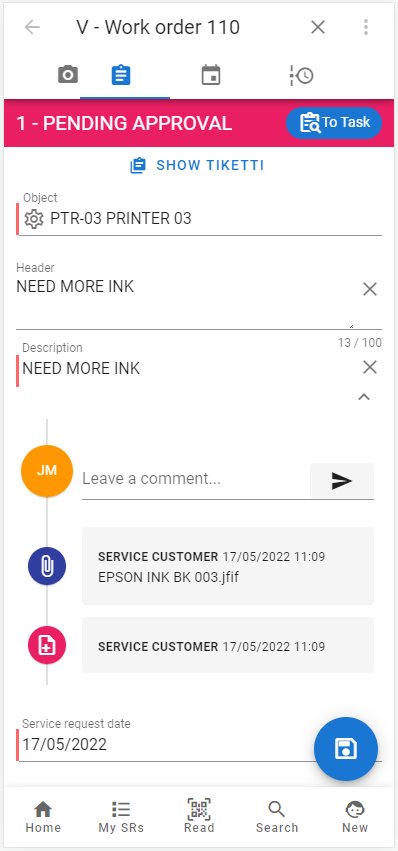
ENTERPRISE
ENTERPRISE
CORRECTIVE MAINTENANCE
STARTER
ANEO Zero Starter contains basic functionalities and features needed to manage nonrecurring corrective repair work orders and related tasks.
Maintenance planners create new work orders based on service requests and other notifications. The planner fills in the basic information about the maintenance job to be done and allocates the completion date and can take a photo with a mobile device or select an attachment already saved in ANEO Zero or add a new attachment from the computer.
Tasks are allocated to maintenance teams or team members. ANEO Zero will track the time it takes to complete the tasks. The job executor can start the task and pause it, if necessary, in which case the time tracking will also be stopped. Finally, the job executor writes or dictates a report and acknowledges the task as completed, which also ends the working time tracking.
PROFESSIONAL
ANEO Zero Professional includes the basic functionalities and features of Starter. In addition, instructions and work permits can be added and cost management is enabled.
Maintenance planners can quickly create new work orders by copying a similar work order created on the same object. They can also share a link to the work order via email. Before execution the planner can change the status of the work order and add comments and working hours.
Job executors can transfer the position of the object in question in the equipment hierarchy if they physically relocate the equipment, e.g. to a repair shop for maintenance.
The foreman can cancel the work order execution or, if necessary, return it back to be planned and executed again.
ENTERPRISE
ANEO Zero Enterprise includes the functionalities and features of Starter and Professional. In addition, Enterprise enables the phasing of work orders and equipment swap in connection with repair work orders.
The maintenance planner can phase the repair work, to which he can attach, i.e. subordinate, other work orders. Acknowledging a phased work, i.e. a project, as completed also acknowledges other sub-jobs attached to the phased work as completed.
Repair work orders can also be accompanied by equipment swap. Equipment that is to be removed from use or separated for maintenance can be replaced by a substitute equipment that is in working condition waiting for action in the warehouse. The maintenance history of the equipment follow the equipment when swapped.
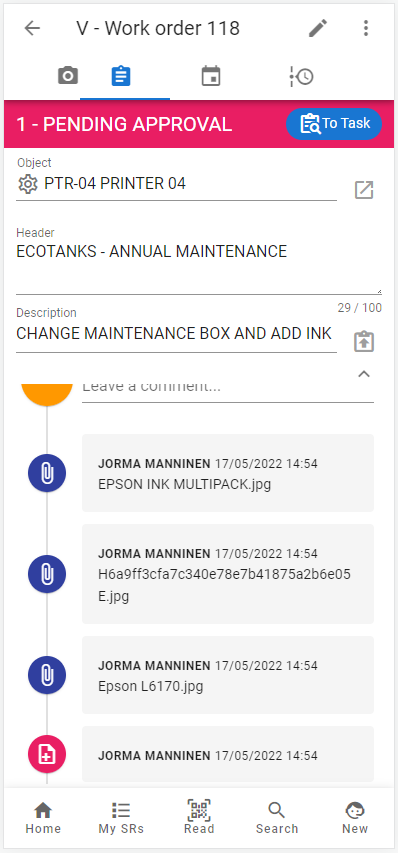
STARTER
STARTER
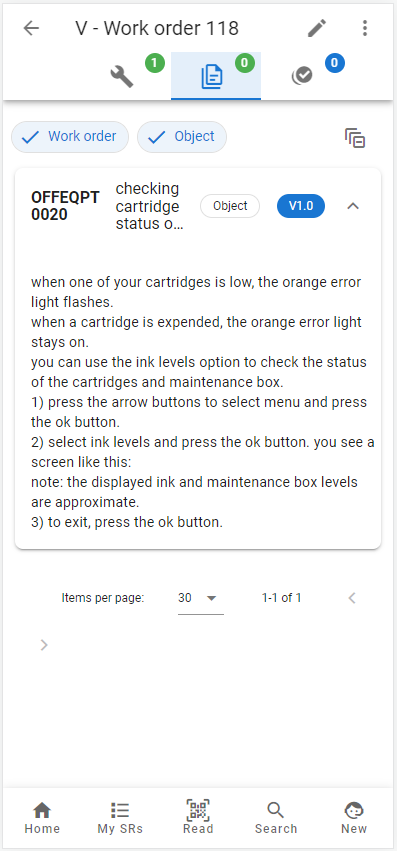
PROFESSIONAL
PROFESSIONAL
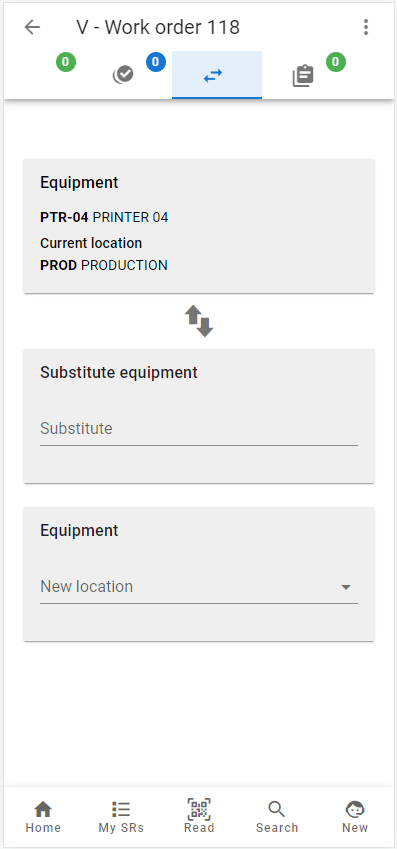
ENTERPRISE
ENTERPRISE
PREVENTIVE MAINTENANCE
STARTER
ANEO Zero Starter includes the functionalities and features needed to manage preventive maintenance (PM) work orders.
Maintenance planners can create predetermined PM work orders and set the recurrence based on time intervals. The work orders can be set to recur on a daily, weekly or fixed weeks basis. ANEO Zero creates upcoming PM tasks automatically based on the original PM work order.
Maintenance planners and installers can take photos and attach attachments for advance maintenance from the memory of a mobile device or computer or select attachments previously saved in Zero.
PM task executors who have participated in the execution of the PM tasks can report working hours individually. ANEO Zero tracks the wrench time automatically for every PM task executor separately.
PROFESSIONAL
ANEO Zero Professional includes all the functionalities and features of the Starter. In addition, maintenance planners can set the recurrence of PM tasks based on the equipment utilization.
Instructions can also be managed and attached to PM work orders. Maintenance task executors can read the attached instructions and documents before or during the execution of the PM task.
Spare parts and materials can be issued to PM Tasks and returned to the warehouse, if the inventory management software module is enabled.
Cost management is another additional functionality for Professional users, who can track the cost of reported working hours and used spare parts and materials. Cost reports can be retrieved from ANEO Zero based on various search criteria.
ENTERPRISE
ANEO Zero Enterprise includes the functionalities and features of the Starter and Professional. In addition, maintenance planners can set the recurrence of PM tasks based on the asset condition data or predictions.
Maintenance planners can also bundle PM work orders under a recurring route work order that sets the recurrence for all bundled PM tasks. The bundled PM work orders and tasks must be executed before the route work order can be completed.
Work permits of PM work orders is also enabled for the Enterprise users. Maintenance planners can add required work permits to PM work orders.
At Enterprise level it is also possible to integrate the work order management software module with other systems like payroll systems, who can import reported and approved working hour records from ANEO Zero for payroll calculation and payment.
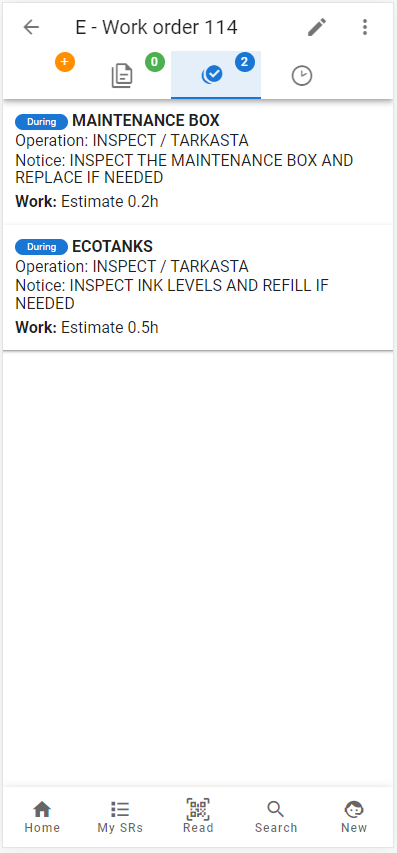
STARTER
STARTER
ALLOCATION
RECURRENCE
TIMELINE
MATERIALS*
ATTACHMENTS
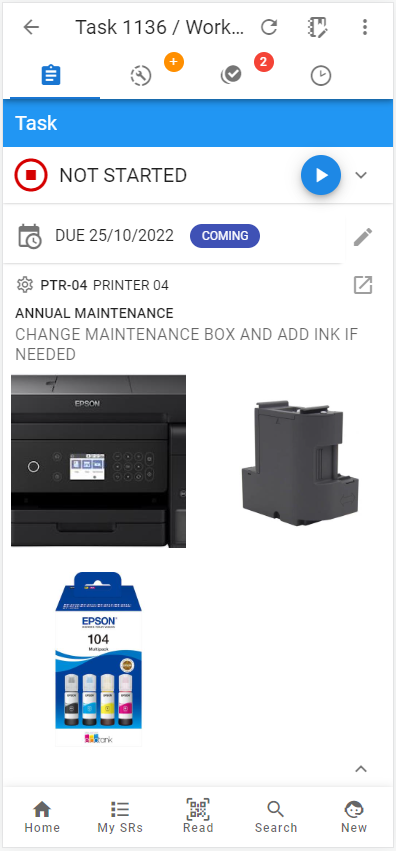
PROFESSIONAL
PROFESSIONAL
ALLOCATION
RECURRENCE
TIMELINE
MATERIALS*
INSTRUCTIONS
ATTACHMENTS
METER-BASED RECURRENCE
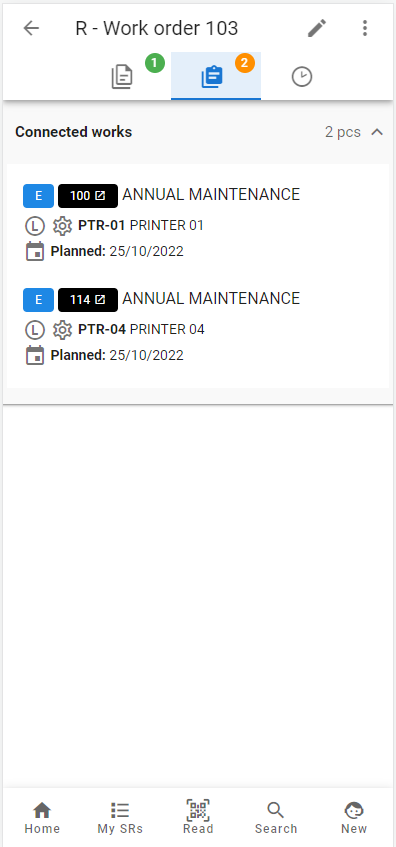
ENTERPRISE
ENTERPRISE
ALLOCATION
RECURRENCE
TIMELINE
MATERIALS*
INSTRUCTIONS
ATTACHMENTS
METER-BASED RECURRENCE
ROUTE WORK ORDERS
INSPECTION
STARTER
ANEO Zero Starter includes the basic functionalities and features needed to manage recurring and nonrecurring inspections. Maintenance planners can create check objects and develop check lists for inspection work orders.
Inspectors can take and add photos or other attachments to the inspection work order during the execution of the inspection task.
Inspectors write or dictate the inspection report separately for each check object during the execution of the inspection tasks. Working hours are reported and individual inspection times are tracked automatically.
PROFESSIONAL
ANEO Zero Professional includes the functionalities and features of the Starter. In addition, maintenance planners can add instructions to the work orders and cost management is also enabled.
Inspectors can take and add photos or other attachments to the individual check objects separately.
Inspectors can create new work orders from every check object, when the detect equipment faults or machine failures during the execution of inspection tasks. ANEO Zero will copy information from the original inspection work order to the new work order.
ENTERPRISE
ANEO Zero Enterprise includes the functionalities and features of the Starter and Professional. In addition, maintenance planners can add free input fields for every individual check object separately to enable the collection of measurements and data from the objects of inspection. Data types of free input fields are text, numeric, and logical.
Customized inspection reports can be developed for different types of inspection work orders for printing and signing if needed. Report templates can be personalized according customer needs and requirements.
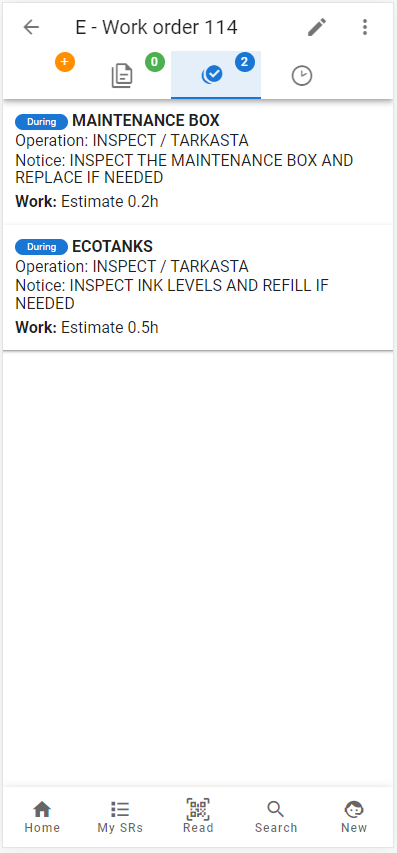
STARTER
STARTER
ALLOCATION
ATTACHMENTS
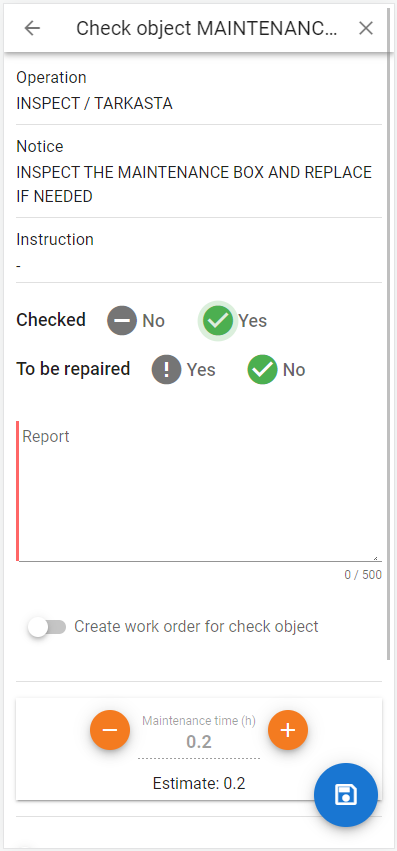
PROFESSIONAL
PROFESSIONAL
ALLOCATION
ATTACHMENTS
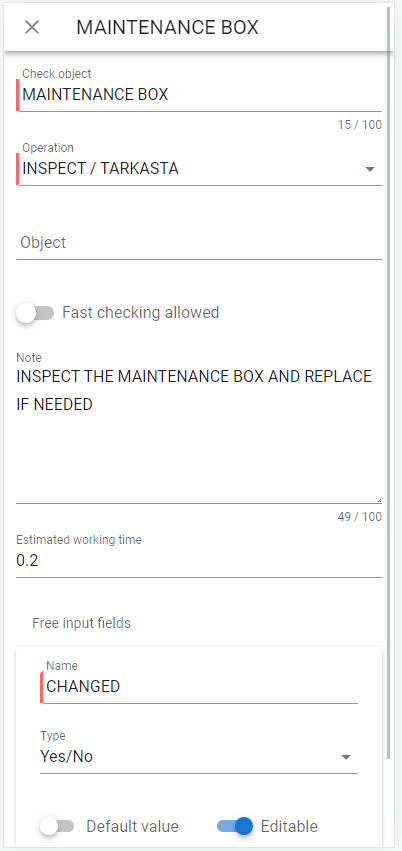
ENTERPRISE
ENTERPRISE
ALLOCATION
ATTACHMENTS
ADDITIONAL FUNCTIONALITIES
ANEO Zero Starter, Professional and Enterprise features can be supplemented with additional functionalities and features such as local kind of activity units and inventory management or purchase management software modules.
LOCAL UNITS
INVENTORY
Maintenance planners can add spare parts and materials to work orders. Maintenance task executors can issue spare parts and materials from the warehouse for tasks and, if necessary, return unused items to the warehouse.
PURCHASING
Purchasers can not only order spare parts and materials, but also machinery and equipment.
REPORTING
STARTER
ANEO Zero Starter includes search functions for different types of work orders and tasks as well as maintenance objects, for example.
Administrators can also search for users and maintenance teams and update information and roles if necessary.
In addition, spare part and material items and purchase requisitions and orders can be searched if inventory and purchase management are enabled.
PROFESSIONAL
ANEO Zero Professional includes the functionalities and features of Starter. In addition, data from search result views can be exported to MS Excel files for customizing reports.
It is possible to print preventive and corrective maintenance work orders or tasks on paper or in a PDF file.
The inspection report printing function also enables you to print the reports with inspection check objects and the photos taken or attached to them as attachments to the inspection report.
ENTERPRISE
ANEO Zero Enterprise includes the functionalities and features of Starter and Professional as well as the possibility to order customized report templates for printing purposes.
Inspection results can be printed out as a customized inspection report so that the photos attached to them and the data entered in the free input fields can be printed as parts of the report. Inspection check objects can be classified into different groups based on how the information stored on them is to be printed in the report.
WORK ORDER SEARCH
WORK TIME TRACKING
STARTER
ANEO Zero Starter includes a working time tracking feature, which measures the working time aka "wrench time" spent from the moment the maintenance job executor starts the task until he acknowledges the work is complete.
If necessary, the job executor can also pause the execution and resume it later. If a new task is started before the ongoing task has been completed, the ongoing task is automatically paused, so that wrench time is not accumulated for several tasks at the same time.
PROFESSIONAL
ANEO Zero Professional includes the functionalities and features of the Starter. In addition, inspectors can report working hours spent on each check object separately.
The working hours reported by the employees can be automatically approved or they can first be checked and approved by foremen, only after which the approved working hours entries also become work costs. In addition, working hours and costs can be searched using the cost search function.
ENTERPRISE
ANEO Zero Enterprise includes the functionalities and features of Starter and Professional. In addition external payroll systems can be integrated with ANEO Zero.
ANEO Zero Enterprise includes also the so-called time clock or clock card feature. Working time monitoring starts when the employee presses the start button on the home screen of the mobile device or computer. At the end of the day, the employee stamps the time clock again, when the working time tracking ends.
WORK TIME REPORTING
"Businesses struggle with their aging assets, so we developed ANEO Zero, the agile cloud-based maintenance system, that helps you keep your property, plant, and equipment in good working order and your operations up and running 24/7."
- Markku Lyyski, Aneo Software Oy
SEND EMAIL
ANEO
CUSTOMERS
ANEO BLOG
What are Maintenance Types?
Some businesses are still running their fixed operating assets to failure and their maintenance is...